The pharmaceutical industry demands a strict hygiene protocol to maintain the safety and quality of…
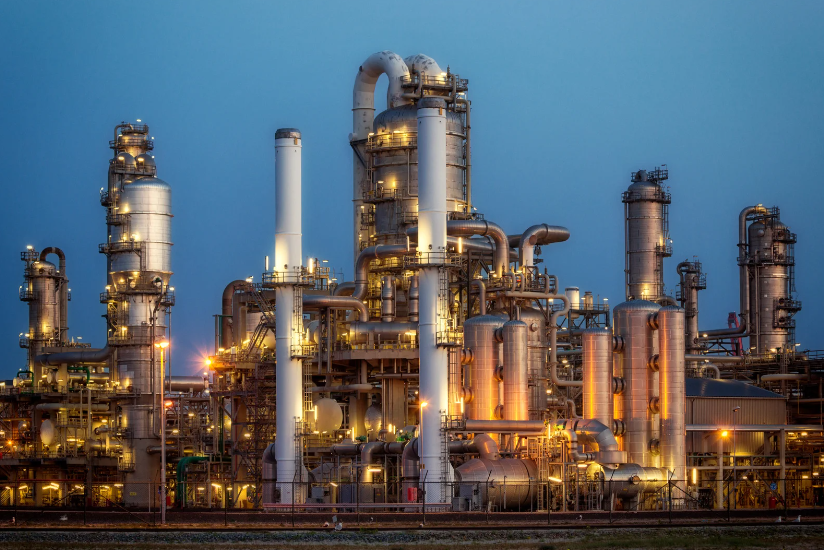
A common question faced by process engineers using industrial static mixers is what is the right pressure drop for the best mixing results? Pressure drop is the difference in pressure before and after a static mixer, caused by the resistance of the mixer to the flow of liquid or gas passing through it. In this article, we will discuss why a lower pressure drop is better and how it can positively impact your process.
What Are Static Inline Mixers?
Static inline mixers are a type of mixing equipment used to combine two or more substances together uniformly. These mixers work by creating fluid forces that blend the substances as they pass through stationary elements, including a series of baffles or vanes. Static mixers are used in a wide range of industries, including chemical, pharmaceutical, water and wastewater treatment, and petrochemicals.
One of the main advantages of static inline mixers is their ability to provide efficient and effective mixing through pressure differentials/drops without the need for external power sources or additional equipment. They also blend and combine materials more accurately and are available in a variety of configurations to suit different industrial mixing applications.
So, Do You Need High Pressure For Good Mixing Results?
No. A widely held misconception is that a high-pressure drop is required for good mixing. However, in reality, you can have good mixing with a low-pressure drop. This is better as it means that the mixer being used is more efficient. You can also have a high-pressure drop with very poor mixing!
- High mixture quality with lower pressure drop = high efficiency.
- High mixture quality, but with high-pressure drop = poor efficiency.
Energy Efficiency
Energy efficiency is one of the major concerns in any industrial process, for both sustainability and cost management reasons. A higher pressure drop means that more energy is required to push the liquid or gas through the mixer. This results in increased energy consumption, which can negatively impact the efficiency of your process. By choosing products with a lower pressure drop, you can therefore minimise the energy required to transport the fluid, thus reducing your operational costs.
Pump Size
The size of the pump you need is another factor affected by the pressure drop. An additional energy requirement means that a larger and more powerful pump is needed to maintain your desired flow rate. This not only increases the capital cost of your system but also raises the operating expenses for a longer duration. By choosing products with a lower pressure drop, you can often get the same results from a smaller pump, resulting in lower equipment and operating costs.
Pressure Tolerance
Suppose the pressure drop is too high in the system. In this case, it may require additional equipment or modifications to the existing system to accommodate the higher pressure drop without risk of damage, adding further costs and complexity to the process. For example, if the pressure drop is caused by the narrow bore of the mixer, the modification may involve replacing the existing mixer with a broader bore. By choosing equipment with a lower pressure drop, you can often avoid the cost and complexity of system modifications, streamlining your process without compromising on quality.
A lower pressure drop also helps you achieve a more efficient uniform mixing of the liquids or gases, delivering improved product quality. With a uniform mixture quality, there is a higher probability of the fluid undergoing complete homogenization, and the chemical reaction can be more precisely controlled.
Contact Us
Contact Statiflo today to find out more about our range of static in-line mixers, and how a lower-pressure drop can help boost efficiency and productivity throughout your process.
Image Source: Canva