Chemical Dosing Lances / Injection Lances
Statiflo Chemical Dosing Lances / Injection Lances are specifically designed to meet the needs of industry and maximise the mixing potential of Statiflo Inline Static Mixers. They are available to purchase with our Static Mixers or as a standalone product.
Being withdrawable under pressure means that the main line doesn’t have to be completely depressurised in order to remove the dosing lance for maintenance.
Various designs are available including the new XHP (Extra High Pressure) dosing lance which in addition to working with higher pressures than the rest of the Statiflo Chemical Dosing Lance range, uses a threaded wind-out design – as is now required by some sites – to be suitable for the most stringest of health & safety requirements.
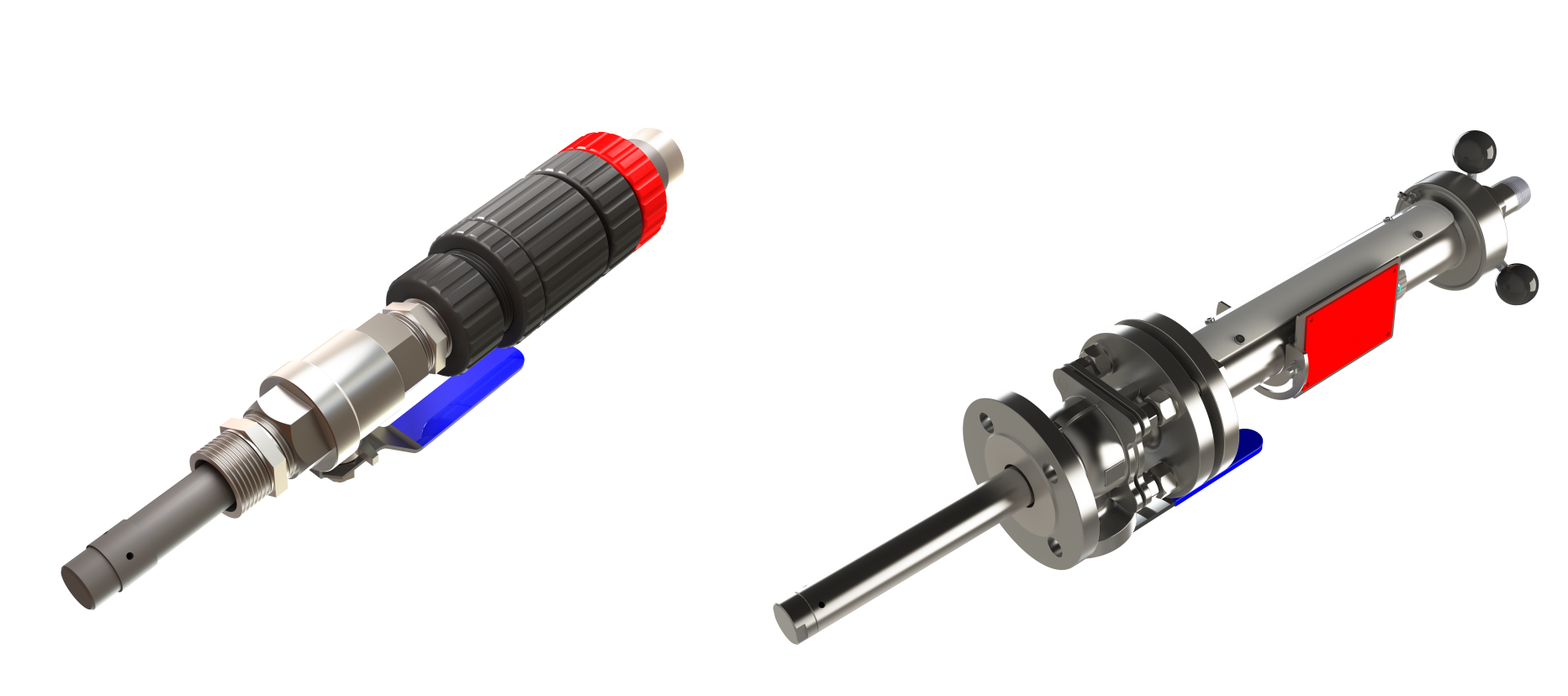
- Available in Low Pressure, High Pressure and Extra High Pressure Designs
Low pressure (LP) pull out/push in design suitable for 10 barg injection pressure – built in uPVC material complete with stainless steel isolation valve. Other materials for isolation valve are available upon request.
High pressure (HP) pull out/push in design suitable for 16 barg injection pressure – built in stainless steel or Hastelloy material and complete with stainless steel isolation valve. Other materials for isolation valve are available upon request.
Extra high pressure (XHP) wind out/wind in design suitable for 25 barg injection pressure – built in stainless steel or Hastelloy material and complete with stainless steel isolation valve. Other materials for isolation valve are available upon request.
- Suitable for Statiflo’s market-leading mixing element designs
Statiflo Injection Lances are built to optimise the performance of our STL or STM element designs with release holes in set in specific locations in order to introduce the additive into the main flow at the optimum location. They can also be supplied as a standalone product.
- Available for most pipe sizes
Suitable for main line diameters from as small as DN100 (4″) with no theoretical upper limit.
- Superior mixture qualities achievable
Designed to optimise the performance on Statiflo Inline Static Mixers and help achieve a Coefficient of Variation (CoV) of 0.05 or less by the discharge of the mixing elements for miscible systems – meaning you can take a representative sample at the downstream end of the mixer.
- Materials to suit your requirements
Available in uPVC, Stainless Steel or Hastelloy to cover you for even the most corrosive injection chemicals.
- Performance Guarantee
If purchased with a Statiflo Inline Static Mixer, your injection lance comes with guaranteed performance. Our static mixer designs have been extensively and rigorously tested under industry-realistic conditions to allow us to guarantee the mixing performance and the head loss across the mixer. If required Statiflo can perform CFD simulations for specific conditions.
- Testing Standards
A full visual inspection is carried out on each unit before it leaves our premises, along with a dimensional check.
- Warranty Period
As standard, Statiflo offers a warranty of 12 months from plant commissioning or 18 months from equipment delivery, whichever is the sooner. Extended warranties can be supplied upon request.
- Spare Parts / Special Tools
Statiflo products have no moving parts there is no requirement for expensive spares or special tools.
- Supervision for Installation and Commissioning
The ‘plug and play’ design means there is no requirement for supervision for installation or commissioning. The extremely simple installation is covered entirely by the Installation, Operation & Maintenance manual supplied with each order.
If you would feel more comfortable having guidance on-site, Statiflo can send one of our highly qualified engineers to guide and supervise the installation to give you the confidence that everything is done correctly.
Downloads
Mixer Sizing Questionnaires
Product Brochures
Application Notes
Gas dispersion system for the ozonation of drinking water
Gas Dispersion System: The inline dispersion of a gas in a large volume of liquid…
Case Study
Process with highly viscous polymer melts
Problem A “man-made” fiber spinning plant produces thousands of individual threads simultaneously. All threads come…